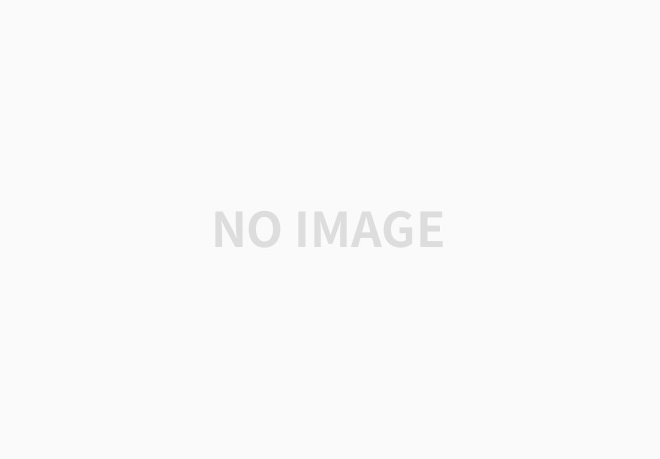
4차 산업혁명을 거치면서 발전된 IT기술들은 제조업에도 상당한 영향을 미췄는데요, 그 결과물 중 하나가 스마트 팩토리라고 할 수 있습니다. 이번 포스팅에서는 스마트 팩토리에 대해 알아보고 국내외 사례를 간단히 알아보겠습니다.
스마트팩토리?
스마트 팩토리(smart factory)는 제조업 분야에서 생산과정에 ICT라고 불리는 (Information and Communications Technologies) IT기술이 접목되어 만들어진 혁신적인 미래 공장입니다.
특히 스마트팩토리는 IoT 기술을 (Internet of Thing : 사물에 센서 등을 연결하여 사물 간 혹은 사물과 관리자 간 소통할 수 있게 하는 기술) 기계 및 설비에 적용한 것이 주요 특징입니다.
이를 통해 공장 내 데이터의 실시간 수집과 교환을 가능케 하고 고객만족과 품질관리 , 생산효율성 향상을 목표로 합니다. 스마트 팩토리는 단순 제조현장뿐만 아니라 설계와 유통과정을 포괄한 다양한 분야에 적용됩니다.
스마트 팩토리는 스마트센서, CPS (Cyber Physical System : 물리적 세계의 정보들을 디지털 상의 정보로 교환하고 이를 활용하는 기술), 3D 프린팅, 에너지 절감 기술을 포함한 생산시스템 혁신기술과 IoT, 클라우드. 빅데이터, 홀로그램, AI 등의 ICT 기술을 포함합니다.
특히 AI는 과거의 데이터로부터 학습한 최적의 답안으로 공장 내 여러 문제를 실시간으로 처리합니다. 인간은 숙련정도에 따라 능력치가 매우 상이하고 결정적으로 반드시 휴식을 취해야 하면서 매시간 집중력이 다른데 반하여 AI는 위의 문제들과 상관이 없고 수많은 변수들을 최적화하여 문제를 처리합니다.
위에서 언급한 기술들은 스마트 팩토리 내에 다양한 제조단계에 적용됩니다. 우선 제품의 수요 예측 단계에서 빅데이터를 이용하여 정확한 수요예측을 합니다.
또한 제품 설계 시에는 홀로그램이나 3D 프린팅을 적용하여 시제품을 제작하여 다품종 소량생산을 가능하게 합니다. 제품 제조단계에는 현재 자동화 생산관리시스템이 스마트 통합 공정을 통해 실시간 생산관리될 것이며, 마지막 유통단계에는 클라우드를 이용하여 유통시스템 구축에 필요한 데이터를 중앙 화하여 비용을 절감하고 능동적인 유통관리 시스템을 구축할 것입니다.
스마트 팩토리 국내 사례
- LS산전
- 포스코
- 전우정밀
- 신성이엔지
- 대성 아이엔지 등
대표적으로 LS그룹의 LS산전이 있는데 수요예측시스템을 적용한 생산방식의 스마트팩토리 시스템을 구축하여 설비 대기 시간을 50퍼센트 정도 감축하였고, 생산율 약 60퍼센트, 에너지 사용량 약 60퍼센트 이상 절약, 불량률 6PPM 감소 등의 성과 달성을 하였습니다.
다음으로 국내 최대 철강기업 포스코가 있습니다. 포스코는 대표적인 국내 스마트 팩토리 기술도입 기업으로 손꼽힙니다. 포스코는 고유의 스마트 플랫폼 ‘포스프레임’‘포스 프레임’을 이용하여 ‘스마트 제철소’라는 이름으로 각 공정에 스마트 팩토리를 적용하였습니다. ‘포스 프레임’은포스프레임’ 세계 최초 연속제조 공정 스마트 팩토리 플랫폼으로 이것으로 전 공장의 데이터 수집, IoT, 빅데이터, Ai기술을 이용해 데이터 학습 및 공정 최적화, 공정제어를 실행하였습니다.
이외에도 전우 정밀, 신성이엔지, 대성 아이엔지 등의 기업이 스마트 팩토리를 적용하여 성공한 국내 사례입니다
스마트팩토리 해외 사례
- 독일의 지멘스그룹
- 아디다스
독일의 지멘스 그룹이 스마트 팩토리의 대표주자로 언급됩니다. 지멘스는 중공업, 철도사업 및 가전제품 제작 사업을 영위하는 종합 엔지니어링 그룹입니다. 특히 지멘스의 암베르크 공장은 높은 생산율과 품질관리를 통해 성공적인 결과를 도출했습니다.
특히 지멘스 그룹은 디지털 트윈이라는 기술을 사용하였는데 디지털 트윈 기술이란 시제품과 똑같은 모양을 디지털 상에서 구현하여 발생 가능한 변수나 문제들을 사전에 파악하여 생산성을 높이는 기술입니다. 이를 통해 상당한 비용 절감을 이루어냈습니다.
또한 우리가 잘 아는 기업 아디다스도 신발 제조에 3D 프린팅과 첨단 설계 기술을 도입했고 다양한 스마트 팩토리의 기술을 접목하여 리드타임은 6주에서 24시간 이내로 생산인력을 1/60 수준으로 감축시켰다고 합니다.
'알면 쓸모있는 지식' 카테고리의 다른 글
미수금 개념 및 미수거래 방법과 반대매매 당하지 않는 방법 (0) | 2021.12.14 |
---|---|
예수금, 증거금과 독특한 주식 거래 시스템에 대해 알아보자 (0) | 2021.12.14 |
헷갈리는 2차전지 용어 모형, 재료별 종류 및 특징을 간단하게 정리 (0) | 2021.11.26 |
[신종 보이스피싱] 정부지원자금 미신청 문자로 서민금융진흥원 및 은행사칭사례 (0) | 2021.11.25 |
모바일한경 태블릿 이벤트 갤럭시 탭 공짜로 얻고 경제신문도 구독 (0) | 2021.11.12 |
댓글